هنالك مقولة شائعة في عالم التصنيع وهي
الكفاءة هي الملك.
تسعى مصانع الإنتاج إلى تحسين كل جانب من جوانب عملياتها لضمان أقصى قدر من الإنتاج بأقل قدر من النفايات. ومع ذلك، حتى العمليات الأكثر تخطيطًا وتبسيطًا يمكن أن تواجه تحديات، وأحد أهم هذه التحديات هو عنق الزجاجة.
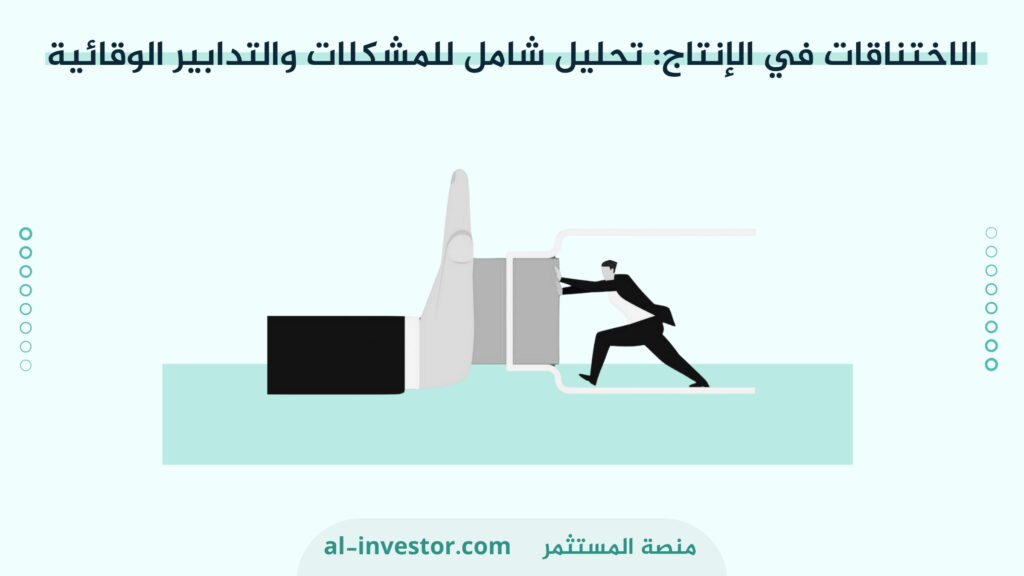
تعريف الاختناقات في مصانع الإنتاج
يشير عنق الزجاجة في مصنع الإنتاج إلى نقطة في عملية التصنيع حيث يتباطأ تدفق الإنتاج أو يقيد، مما يؤدي إلى انخفاض في الإنتاج الإجمالي. تخيل طريقًا سريعًا تتدفق فيه حركة المرور بسلاسة حتى تصل إلى جسر ضيق؛ وفي تلك المرحلة، يتباطأ تدفق السيارات بشكل كبير، مما يؤدي إلى تراكم حركة المرور خلفها. وبالمثل، في بيئة المصنع، يمكن أن يحدث اختناق في مراحل مختلفة من الإنتاج، مما يعيق التدفق السلس للمواد ويقلل الكفاءة ويزيد التأخير في الإنتاج والتكلفة أيضًا.
يؤثر عنق الزجاجة كثيرًا على تدفق التصنيع، ويزيد من وقت وتكلفة الإنتاج، وتزداد قابلية تعرُض الشركات لعنق الزجاجة أو للاختناق عندما تبدأ عملية إنتاج منتج حديث، نظرًا لاحتمال وجود عيوب في العملية، فيجب على الشركة في هذه الحالة تحديدها وتصحيحها، ويحتاج ذلك إلى مزيدًا من التدقيق والضبط، وتهتم إدارة العمليات بالتحكم في عملية الإنتاج، وتحديد الاختناقات الممكنة قبل حدوثها، وإيجاد حلول فعّالة.
على سبيل المثال، لنفترض أن شركة تصنيع أثاث تنقل المعادن والخشب والمواد الخام الأخرى إلى منشأة الإنتاج، ثم تتحمل تكاليف الآلات والعمالة اللازمين لإنتاج الأثاث وتجميعه، وعند اكتمال الإنتاج، تُخزن البضائع الجاهزة في المخزون، ثم تحول تكلفة المخزون إلى تكلفة البضاعة المباعة Cost Of Goods Sold عند بيع الأثاث للعميل، والتي يُشار إليها اختصارًا COGS.
إذا كان هناك عنق زجاجة في بداية الإنتاج، فلن يتمكن صانع الأثاث من نقل ما يكفي من المواد الخام إلى العملية، مما يعني أن الآلات ستبقى في وضع الخمول، وسيتلقى العمال أجرًا دون عمل مُنتِج، مما يُشكّل حالة من نقص استثمار الموارد، ويؤدي ذلك إلى زيادة تكلفة الإنتاج، بالإضافةً إلى ضياع فرصة بديلة كبيرة ممكنة، بالإضافة إلى عدم شحن البضائع الجاهزة إلى العملاء في الوقت المحدد.
إقرأ أيضًا: طرق لزيادة الكفاءة الانتاجية في العمل
تحديد الاختناقات
تظهر الاختناقات بأشكال مختلفة داخل بيئة الإنتاج. وقد تنشأ بسبب القيود المفروضة على الآلات، أو القوى العاملة، أو توافر المواد، أو عدم كفاءة العمليات، أو حتى التحديات اللوجستية. يمكن أن تكون تداعيات الاختناقات التي لم تتم معالجتها شديدة، بما في ذلك انخفاض الإنتاجية، وزيادة المهل الزمنية، وارتفاع تكاليف التشغيل، وتدهور الجودة، واستياء العملاء. ولذلك، فإن القدرة على تحديد الاختناقات وتصحيحها أمر بالغ الأهمية لضمان سلاسة العمليات والحفاظ على ميزة تنافسية في السوق.
استراتيجيات تحديد حالات الاختناق في مصانع الانتاج
يتطلب تحديد الاختناقات ومعالجتها بشكل فعال فهمًا شاملاً لسير عمل الإنتاج، وتحليل البيانات الدقيقة، واتخاذ القرارات الإستراتيجية وعمومًا يمكننا اتخاذ القرارات التالية لتحديد حالات عنق الزجاجة في عمليات الإنتاج:
- رسم خرائط العمليات وتحليلها
ابدأ برسم عملية الإنتاج بأكملها، بدءًا من تناول المواد الخام وحتى تسليم المنتج النهائي. تحديد كل مرحلة والعمليات الفرعية والمدخلات والمخرجات والتبعيات. استخدم أدوات تعيين العمليات مثل المخططات الانسيابية أو خرائط تدفق القيمة لتصور سير العمل وتحديد مناطق الاختناق المحتملة.
- جمع البيانات ومراقبتها
تنفيذ آليات قوية لجمع البيانات لجمع البيانات في الوقت الفعلي حول مقاييس الإنتاج مثل أوقات الدورات ومعدلات استخدام الآلة ومستويات المخزون والمهل الزمنية. استخدم أنظمة تنفيذ التصنيع (MES) وأجهزة الاستشعار وأجهزة إنترنت الأشياء لتتبع أنشطة الإنتاج ومؤشرات الأداء. تحليل البيانات التاريخية للكشف عن الأنماط والاتجاهات والشذوذات التي قد تشير إلى حدوث اختناقات.
- مقاييس الأداء ومؤشرات الأداء الرئيسية
تحديد مؤشرات الأداء الرئيسية (KPIs) ذات الصلة بتحديد الاختناقات، مثل معدلات الإنتاجية، واستخدام القدرات، ومستويات مخزون العمل الجاري (WIP)، وكفاءة دورة الإنتاج (PCE). راقب هذه المقاييس بانتظام وقم بوضع معايير لقياس الأداء مقابل الأهداف المحددة مسبقًا.
- المحاكاة والنمذجة
استخدم برامج المحاكاة وتقنيات النمذجة لمحاكاة سيناريوهات الإنتاج المختلفة وتقييم تأثير الاختناقات المحتملة. قم بإجراء تحليلات “ماذا لو” لتقييم كيفية تأثير التغييرات في المتغيرات مثل قدرات الماكينة أو تخصيص القوى العاملة أو جداول الإنتاج على الإنتاجية الإجمالية وتحديد السيناريوهات المعرضة للاختناق.
اعتنق مفهوم جيمبا، الذي يتضمن الذهاب إلى مكان العمل الفعلي لمراقبة العمليات بشكل مباشر. قم بإجراء جولات Gemba بانتظام للتفاعل مع العاملين في الخطوط الأمامية، وفهم تحديات سير العمل، وجمع الأفكار، وتحديد الاختناقات التي قد لا تكون واضحة من تحليل البيانات وحدها.
- تحليل السبب الجذري
عند اكتشاف الاختناقات، قم بإجراء تحليل السبب الجذري (RCA) للتعمق أكثر في العوامل الأساسية التي تساهم في الاختناق. استخدم تقنيات مثل مخططات هيكل السمكة (مخططات إيشيكاوا)، أو تحليل الأسباب الخمسة، أو مخططات باريتو لتحديد الأسباب الجذرية مثل أعطال المعدات، أو اختناقات سير العمل، أو فجوات المهارات، أو نقص المواد.
- فرق تعاونية متعددة الوظائف
تشكيل فرق متعددة الوظائف تضم مديري الإنتاج والمهندسين ومحللي البيانات والعاملين في الخطوط الأمامية لتحديد الاختناقات ومعالجتها بشكل تعاوني. تشجيع التواصل المفتوح وتبادل المعرفة وجلسات العصف الذهني لتوليد حلول مبتكرة وأفكار التحسين المستمر.
استراتيجيات إدارة الاختناقات
- تحسين تخصيص الموارد
إحدى الاستراتيجيات الأساسية لإدارة الاختناقات هي تحسين تخصيص الموارد. وهذا يشمل الآلات والقوى العاملة والمواد. ومن خلال تحليل جداول الإنتاج، وتوقعات الطلب، وقيود القدرات، يمكن للمصانع تخصيص الموارد بكفاءة لتقليل الاختناقات. وقد يتضمن ذلك تحديد أولويات المهام الحاسمة، وموازنة أعباء العمل، والتأكد من استخدام الموارد إلى أقصى إمكاناتها.
- تنفيذ أدوات التخطيط المتقدمة
يمكن أن يساعد استخدام أدوات التخطيط والجدولة المتقدمة بشكل كبير في إدارة الاختناقات. تساعد هذه الأدوات في إنشاء جداول إنتاج محسنة، وتحديد الاختناقات المحتملة مسبقًا، ومحاكاة سيناريوهات مختلفة لتقييم تأثيرها. ومن خلال الاستفادة من التكنولوجيا، يمكن للمصانع اتخاذ قرارات مستنيرة، وضبط الجداول الزمنية ديناميكيًا، وتخفيف الاختناقات بشكل استباقي.
- تبني مبادئ التصنيع الخالي من الهدر
تعتبر مبادئ التصنيع الخالي من الهدر، مثل الإنتاج في الوقت المناسب (JIT)، وتقليل النفايات، والتحسين المستمر، مفيدة في إدارة الاختناقات. يساعد JIT في تقليل مستويات المخزون، وتقليل المهل الزمنية، وضمان التدفق المستمر للمواد، وبالتالي منع الاختناقات الناجمة عن نقص المواد أو المخزون الزائد. تعمل مبادرات التحسين المستمر، مثل أحداث كايزن، على تمكين الفرق من تحديد الاختناقات والقضاء عليها بشكل منهجي.
- الاستثمار في الأتمتة والتكنولوجيا
الاستثمار في الأتمتة والتكنولوجيا يمكن أن يحدث ثورة في إدارة الاختناقات. يمكن للأنظمة الآلية التعامل مع المهام المتكررة بدقة وسرعة، مما يقلل الاعتماد على العمل اليدوي ويخفف من الاختناقات الناجمة عن قيود القوى العاملة. بالإضافة إلى ذلك، تعمل تقنيات مثل الصيانة التنبؤية، وأجهزة استشعار إنترنت الأشياء، وتحليلات البيانات في الوقت الفعلي على تمكين الصيانة الاستباقية، وتحسين أداء المعدات، ومنع التوقف غير المخطط له، والذي يمكن أن يشكل اختناقًا كبيرًا.
- تدريب الموظفين
يعد التدريب المتبادل للموظفين عبر الأدوار والمهام المختلفة بمثابة نهج استراتيجي لإدارة الاختناقات. ومن خلال وجود قوة عاملة مرنة يمكنها التكيف مع المتطلبات المتغيرة، يمكن للمصانع ضمان استمرارية العمليات حتى في حالة عدم توفر عمال ماهرين محددين. ويعزز التدريب المتنوع أيضًا ثقافة التعاون وتبادل المعرفة وحل المشكلات، وهي أمور ضرورية لمعالجة الاختناقات بشكل فعال.
- تعزيز رؤية سلسلة التوريد
يعد التعاون الوثيق مع الموردين وتعزيز رؤية سلسلة التوريد أمرًا بالغ الأهمية لإدارة الاختناقات. ومن خلال تحسين الاتصالات، وتبسيط الخدمات اللوجستية، وتنفيذ أنظمة المخزون التي يديرها البائع (VMI)، يمكن للمصانع تقليل المهل الزمنية، وتقليل نقص المواد، وتعزيز الاستجابة للطلبات المتغيرة. تتيح سلاسل التوريد الشفافة تخطيطًا أفضل، وتقليل الاضطرابات، وتخفيف الاختناقات الناجمة عن عدم كفاءة سلسلة التوريد.
- المراقبة والتحسين المستمر
تعد المراقبة المستمرة لمقاييس الإنتاج ومؤشرات الأداء الرئيسية (KPIs) ولوحات معلومات الأداء أمرًا ضروريًا لإدارة الاختناقات. توفر تحليلات البيانات في الوقت الفعلي رؤى حول أداء الإنتاج، وتحدد الاختناقات على الفور، وتمكن من اتخاذ القرارات المستندة إلى البيانات. ويضمن تنفيذ المراجعات المنتظمة وتدقيق الأداء والإجراءات التصحيحية معالجة الاختناقات بشكل استباقي وتحسين العمليات باستمرار لتحقيق الكفاءة.
عنق الزجاجة والقدرة الإنتاجية
يؤثر عنق الزجاجة أو الاختناق على مستوى القدرة الإنتاجية التي يمكنها للشركة تحقيقها كل شهر، ويفترض مفهوم القدرة النظرية Theoretical Capacity أن الشركة تستطيع إنتاج بأقصى طاقتها في كل الأوقات، كما يفترض عدم وجود إجازات للموظفين أو أعطال في الآلات.
تستخدم معظم الشركات القدرة العملية في إدارة الإنتاج نظرًا لأن مفهوم القدرة النظرية ليس واقعيًا، وتفترض القدرة العملية حدوث عُطل في الآلات واستقطاع وقت لإصلاحه، وحصول الموظفين على إجازة، وتؤمن القدرة العملية مجالًا لتشغيل العمليات المتنوعة بكفاءة دون تعطل، يُؤدي تخطي مجال العمل الأمثل، إلى زيادة مخاطر حدوث اختناق بسبب حدوث عطل أو أكثر في العمليات.
في حال وجدت الشركة أن قدرتها الإنتاجية غير كافية لتلبية أهدافها الإنتاجية، ستجد لديها عدّة خيارات يمكن تطبيقها، فيمكن أن تُقرر إدارة الشركة خفض أهدافها الإنتاجية لجعلها تتماشى مع طاقتها الإنتاجية، أو تستطيع العمل على إيجاد حلول تمنع الاختناقات وتزيد الإنتاج في نفس الوقت، تستعمل الشركات غالبًا أساليب وأدوات تخطيط متطلبات القدرة CRP لتحديد أهداف الإنتاج وتحقيقها.
يمكن أن يسبب الاختناق أيضًا إلى حدوث تباينًا في المواد إذا تعرضت المواد لأي أضرار أو تلف مُمكن نتيجة بقائها على أرضية المصنع انتظارًا لاستخدامها في الإنتاج، ويمكن حلّ الاختناقات من خلال زيادة استثمار القدرات الإنتاجية، وإيجاد موردين جدد، وأتمتة عمليات الأعمال ووضع توقعات أفضل لمعدل طلب المستهلكين.
دراسة حالة: نظام إنتاج مصانع شركة تويوتا اليابانية
وفي الوقت الذي كانت فيه عملية إعادة البناء بعد الحرب العالمية الثانية تمثل تحدياً هائلاً، واجهت شركة تويوتا مهمة شاقة تتمثل في تنشيط عمليات الإنتاج لديها. وخلال هذه الفترة من الشدائد زُرعت بذور الابتكار، مما أدى إلى ولادة نهج تحويلي يعرف باسم نظام إنتاج مصانع تويوتا.
تتشابك قصة تويوتا مع رحلات القادة ذوي الرؤى مثل Taiichi Ohno وEiji Toyoda. شرع هؤلاء الرواد في السعي لإحداث ثورة في التصنيع من خلال تبني المبادئ التي أصبحت فيما بعد حجر الزاوية في مصانع تويوتا. كان محور نظام إنتاج مصانع تويوتا هو مفهوم الإنتاج في الوقت المناسب. بدلاً من الاعتماد على التوقعات، شجع هذا النظام إنتاج السلع بناءً على الطلب الفعلي للعملاء. أدى هذا النهج المبتكر إلى تقليل مستويات المخزون، وخفض تكاليف التخزين، وإنشاء نظام إنتاج أكثر استجابة.
ومع تطور الرحلة، ظهرت فلسفة الجيدوكا، أو الاستقلال الذاتي، كمبدأ إرشادي. أكدت Jidoka على بناء الجودة في عملية الإنتاج من خلال تمكين العمال من إيقاف خط الإنتاج فور اكتشاف أي خلل أو عيوب. وقد وضع هذا التركيز على الجودة الأساس لسمعة تويوتا فيما يتعلق بالموثوقية والتميز.
عنصر رئيسي آخر في نظام إنتاج مصانع تويوتا كان هيجونكا Heijunka، أو تسوية الإنتاج. ومن خلال موازنة الإنتاج عبر متغيرات المنتجات والفترات الزمنية المختلفة، خففت تسوية الإنتاجمن تقلبات الطلب وتحسين الاستخدام للموارد، مما أدى إلى إنشاء سير عمل أكثر كفاءة. ولكن ربما كان الجانب الأكثر جاذبية في نظام تويوتا هو التزامه بالتحسين المستمر، وهو ما يتجسد في مبدأ كايزن. وشجعت الشركة كل موظف على المساهمة بالأفكار، وحل المشكلات، والسعي إلى تحسينات تدريجية في العمليات، وتعزيز ثقافة الابتكار والتعاون.
لم تكن رحلة نظام إنتاج مصانع تويوتا خالية من التحديات. وعلى طول الطريق، تبنت تويوتا أدوات واستراتيجيات مثل نظام كانبان للجدولة المرئية، ونظام أندون للتغذية الراجعة في الوقت الفعلي، ونظام بوكا-يوكي لتصحيح الأخطاء، ورسم خرائط تدفق القيمة لتحليل العمليات. وأصبحت هذه الأدوات هي الترسانة التي مكنت تويوتا من التغلب على العقبات وتحقيق التميز التشغيلي.
ولم يقتصر نجاح نظام إنتاج مصانع تويوتا وحدها. وإنما امتد تأثيرها عبر الصناعات، مما ألهم المؤسسات في جميع أنحاء العالم لتبني ممارسات التصنيع الخالية من الهدر وتبني روح التحسين المستمر.
إقرأ أيضًا: فهم تكاليف الاحتفاظ بالمخزون لتحسين الربحية
دراسة حالة شركة تسلا Tesla الأمريكية
تنشأ الاختناقات أيضًا عندما ترتفع نسبة الطلب بطريقة غير متوقع، ويتخطى الارتفاع الطاقة الإنتاجية لمصانع الشركة أو مورديها، فمثلًا، عندما بدأت شركة تسلا Tesla إنتاج لأول مرة سياراتها الكهربائية بالكامل، كان هناك طلب عالي جدًا على مركباتها، وكان المحللين قلقين من احتمالية تباطؤ الإنتاج بسبب وجود مشاكل في خط الإنتاج، وفي الواقع، شهدت شركة تسلا اختناقات مستمرة في الإنتاج؛ لحاجتها إلى تصنيع حزم البطاريات المخصصة التي تزود سياراتها بالطاقة.
صرّح حينها إيلون ماسك؛ وهو مؤسس شركة تسلا، تعتمد استطاعة الشركة على توسيع وتنويع منتجاتها اعتمادًا مباشرًا على قدرتها على إنتاج عدد ضخم من البطاريات، للوصول إلى ذلك، افتتحت شركة تسلا مصنع جيجا فاكتوري الكبير في عام 2016، لتصنيع بطاريات الليثيوم أيون والتجمعات الفرعية للمركبات الكهربائية للشركة.
بحلول منتصف عام 2018، ادعت الشركة أن مصنعها كان بالفعل أكبر مصانع لتصنيع البطاريات في العالم، من جهة كمية الجيجا وات GWh المُنتجة في الساعة، وأعلنت الشركة أنه يجب أن تواصل لاستثمار وبناء المزيد من مصانع البطاريات في كل أنحاء العالم لتلبي الطلبات المتأخرة على سياراتها.
الخاتمة
تعرفنا على مصطلح عنق الزجاجة Bottleneck والذي يدل على نقطة اختناق في نظام الإنتاج والتي تحدث عندما يزداد حِمل العمل بسرعة عالية جدًا ولا يمكن لعملية الإنتاج مجاراتها، ويؤدي القصور الناتج عن عنق الزجاجة إلى حدوث تأخير في الإنتاج وزيادة تكلفتها، ويكون لعنق الزجاجة تأثيرًا كبيرًا على تدفق التصنيع، إذ يؤثر على مستوى القدرة الإنتاجية التي يمكنها للشركة تحقيقها كل شهر، وتعرفنا على مثال واقعي على عنق زجاجة.
تعليق واحد
هل يمكن استخدام الذكاء الاصطناعي لتوقع الاختناقات قبل حدوثها؟